- By Emily Newton
- May 15, 2024
- ISA
- Feature
Summary
As more organizations embrace digitization under Industry 4.0, those concerns have grown all the more prevalent. It’s now safe to say that thoughtful redundancy is essential for business continuity.
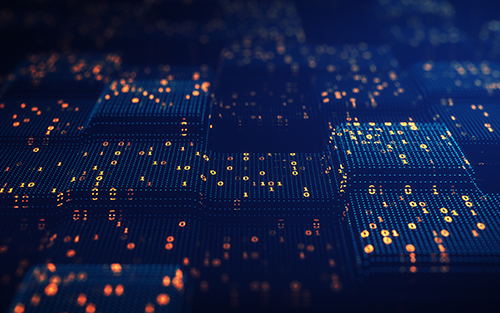
The word “redundant” typically doesn’t carry a positive connotation. That’s especially true in supply chain management, where business practices have trended toward just-in-time (JIT), lean strategies over the past few decades. However, as Industry 4.0 grows, manufacturing redundancy is becoming increasingly important.
Repeated disruptions in the past few years have cast doubt over JIT practices’ resilience. As more organizations embrace digitization under Industry 4.0, those concerns have grown all the more prevalent. It’s now safe to say that thoughtful redundancy is essential for business continuity.
Why redundancy is more important in Industry 4.0
Part of the growing need for manufacturing redundancy stems from the general state of supply chain disruptions. Shocks lasting a month or longer now occur every 3.7 years on average. Geographic concentration—which makes these delays more likely—has also grown, with at least 180 common products coming mainly from a single country. Supplier redundancy would mitigate these single points of failure for added resilience.
Industry 4.0 heightens these concerns in a few ways. First, digitization and automation make supply chains more efficient. While that’s beneficial for many reasons, it makes any slowdowns or stoppages more impactful by comparison. A one-month delay will mean more lost productivity when you typically produce more in a month.
Greater technology reliance may also make manufacturers more prone to disruption. Some businesses have had to halt operations due to failing transformers, as they have more machinery requiring continuous power. Internet of Things (IoT) connectivity exacerbates these issues, as it opens operational technology to failures from network issues.
Similarly, Industry 4.0 initiatives can increase manufacturers’ cyber risks. Once-offline machinery becomes vulnerable to cyberattacks, creating another possible source of disruption. Without proper redundancy, a cyberattack or IT failure could lead to lengthy delays and high costs.
How to ensure manufacturing redundancy
These risks don’t mean Industry 4.0 is more trouble than it’s worth. Rather, they suggest supply chains should take manufacturing redundancy more seriously to fully experience this technology’s benefits. You can achieve this redundancy through a few best practices.
Install redundant hardware
The first step in ensuring redundancy in manufacturing is to implement redundant equipment. In Industry 4.0, that applies to production line machinery and any supporting IoT devices and network infrastructure.
You don’t necessarily need two or more full production lines for every product. However, you should have backups of your most critical components. Using machinery with easy part changeovers to let one line adapt to making a new product will help, too. In terms of network issues, consider using wired connections to supplement wireless ones in case of an outage, and always have a backup power supply for all equipment.
Maintenance practices deserve attention, too. Equipment failure causes 40% of unplanned downtime, so be sure to practice proactive maintenance and keep common replacement parts on hand.
Capitalize on data
While Industry 4.0 heightens redundancy concerns, it also provides some solutions. Most notably, IoT connectivity offers real-time data to uncover issues as they emerge and inform faster responses. This data-driven approach is key to effective redundancy strategies.
Backup hardware and flexible workflows are only useful if you can take advantage of them at a moment’s notice. These quick changeovers require early warnings. IoT applications like predictive maintenance, logistics monitoring and automated risk analysis can provide these alerts, letting you know when it’s time to use backups or adjust operations.
Long-term data is also valuable. Analyze supply chain data to uncover potential weaknesses, such as single points of failure or disruption-prone workflows. Use these insights to inform effective fixes, like adding backup hardware to mission-critical production lines or increasing a factory’s network redundancy.
Practice strong cybersecurity
It’s easy to focus on physical processes in manufacturing redundancy, but these are only part of the whole picture. Amid rising digitization in Industry 4.0, manufacturing has become the most targeted industry for cyberattacks. Consequently, cybersecurity is an essential part of business continuity.
Manufacturers should host IoT devices on separate networks from more sensitive data to minimize the reach of potential breaches. Encrypting all data will likewise reduce the damage. Preventive measures like automated network monitoring, frequent firmware updates, anti-malware software and penetration testing are also crucial.
Redundant practices should apply to cybersecurity as well. Store offline and in-cloud backups of all mission-critical data, and remember to encrypt and monitor these databases, as cybercriminals may target backups. Create a detailed data recovery plan to ensure continuity in the event of a breach.
Increase safety stocks
On a broader scale, supply chains can embrace redundancy by moving away from lean practices. While JIT inventory and production strategies are cost-effective amid normal conditions, disruptions have become too frequent and costly for these methods to be reliable long-term.
Supply chains must instead move toward agile business models, particularly in increasing safety stocks. Having redundancy in high-demand parts and products will mitigate the impact of any upstream supply chain disruptions. This may cost more upfront but reduces losses in the long run.
You don’t necessarily need to apply this practice equally across the entire supply chain. Rather, you can combine agile and JIT practices together to suit different products’ needs. Generally speaking, low-volume, high-volatility items gain the most from agile strategies, while high-volume, low-volatility products can get away with lean inventories.
Embrace distributed sourcing
Supplier diversification is another large-scale application for redundancy in manufacturing. Disruptions can still happen when your suppliers follow all these other steps. Consequently, it’s often safest to have multiple sources for key parts or materials to remove single points of failure.
You can still work with just one supplier and embrace diversification if that partner has multiple locations you can source from. The key is to reduce your reliance on a single facility or region. The global chip shortage of recent years illustrates why. Because Taiwan produces 90% of the world’s advanced semiconductors, shutdowns in the nation led to extensive delays across supply chains.
Start by diversifying your supply of your most critical materials or components before considering this strategy in other areas. As you do, ask potential suppliers about their sources and any dependencies they may have.
Manufacturing redundancy is essential today
“Redundant” shouldn’t be a negative term anymore. Industry 4.0 has brought new attention to supply chain disruptions, requiring a more flexible, agile approach to manufacturing and sourcing.
Ensuring manufacturing redundancy helps organizations make the most of their Industry 4.0 investments. While this may mean some initial spending and disruption, the long-term benefits will be worth it.
This feature originally appeared on ISA Interchange.
About The Author
Emily Newton is the editor-in-chief of Revolutionized, an online magazine celebrating advances in science and technology.
Did you enjoy this great article?
Check out our free e-newsletters to read more great articles..
Subscribe