- By Kenny Marks
- May 17, 2024
- Emerson Automation Solutions
- Feature
Summary
As organizations around the globe launch pilot programs to identify the best lithium battery value chain manufacturing processes, modern, scalable control solutions are key to success.
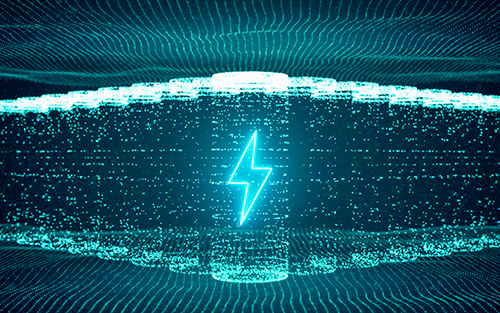
As electric vehicles gain popularity and energy transition initiatives increase demand for energy storage, countries around the globe are seeing a rapid increase in demand for lithium batteries and the raw materials required to manufacture them. Recognizing this opportunity, many manufacturers are pursuing operations to supply more batteries and strengthen supply chains. However, in many world areas, the lithium battery value chain is still developing and maturing, and organizations are building the expertise and process knowledge of how to mine lithium, refine it to the required quality, perform the specialty chemical processing to produce the battery materials, and then build a battery that is safe and effective throughout its lifecycle.
Further complicating this growth is the fact that lithium batteries require raw materials with limited supplies, so the most sustainable supply chains will find ways to create circularity by recycling and reclaiming minerals from used batteries. Reaching these goals will require much trial and error, which is hard to do at production scale.
Navigating complexity
Many manufacturers in the lithium battery value chain are looking for ways to start small with pilots to validate their processes, and to then scale those programs up as they demonstrate success. This strategy, while effective, is different from the more traditional strategy seen in established industries—front-end engineering and design leading to the building of full-scale production facilities. However, scaling from pilot to full-scale production creates its own challenges (Figure 1).
Historically, companies starting pilot projects in processes as complex as those found in the lithium battery value chain would start with built-for-purpose pilot automation solutions, like small programmable logic controllers or PC-based virtual control. However, this strategy comes with trade-offs. Each time a team scales its pilot—from 100 I/O to 1,000+ I/O, all the way up to full production—they will likely need to change and/or modify control platforms repeatedly as they make their way to production scale. Every control platform change is a new project, and projects come with risk. As technologies change and automation needs to be reengineered, processes are more likely to fail. The resulting changes can quickly consume any time and financial benefit of starting with smaller automation solutions.
In addition, scaling not only requires more I/O, but typically also increased functionality. A process with 100 I/O might not immediately need technologies like simulation or advanced process control, but as systems get bigger and more complex, the organization’s needs will expand. Most pilot scale automation solutions are not designed to provide or integrate seamlessly with such advanced technologies, making it hard to add them at later stages.
New technologies for a new era
Fortunately, producers have access to better choices for delivering scalable solutions from pilot to production-scale. Forward-thinking teams are eliminating risk from their pilots by selecting proven, future-proof control technologies designed to scale alongside their projects. Modern, scalable automation platforms can more easily grow to deliver a level of automation customized to the context of the user’s operations, with built-in flexibility to meet changing needs. Best-in-class systems also offer scalable functionality, with all the options of a full production-scale distributed control system (DCS), but in a smaller and more cost-effective package (Figure 2).
Teams using a modern, scalable control system can validate their pilot operations on the exact same hardware and software that will run the production plant they eventually scale to, eliminating the need to start from scratch every time the team grows its operation. Engineers can perform configuration using the same tools, and operators can control the process using the same HMI. Teams have access to full DCS functionality like a process historian, which they can use to easily collect process data for analytics. The most flexible systems also utilize hyperconverged infrastructures, eliminating the need for additional footprint as they grow.
Easier configuration
One key advantage manufacturers are seeing with scalable control solutions for pilots is time saved by configuration reuse. By using class-based configuration, engineers effectively design the process plant’s function library during the pilot. Each of the plant’s processes are designed once, and then turned into classes that can be bulk created each time the system grows. For teams that need very specific control strategies, class-based solutions allow for the creation of a standard configuration library that can be easily leveraged on future projects.
For example, a complex precipitation process might require multiple inputs and outputs to drive effective control for high quality. In a pilot, a team would likely spend a lot of effort understanding how to control that process as effectively as possible. With class-based configuration, once the team has landed on the right control strategy, all the engineering effort can be saved as a class and instantiated quickly in the following projects. Teams also frequently use class-based configuration for operator displays, building graphical elements around operations requirements, and then utilizing them in every iteration of the project.
Intuitive integration
Often, during a pilot, organizations do not need or have the budget for advanced functionality right away. A team is likely not ready to invest in digital twin software for a 100 I/O pilot process, nor to implement advanced control on a process with a few simple loops. However, as processes mature and scale, it is likely the team will need more advanced functionality. Moreover, it is also possible that as market conditions change a producer will need to adapt. In either case, teams will want to be able to quickly add the technologies necessary to stay competitive.
With most pilot scale automation systems, software for historians, advanced control, simulation, and other functionalities requires the addition and integration of external solutions, which is complex and time consuming.
These solutions require additional configuration, and every time the system grows, that configuration needs to be updated.
Forward-thinking organizations are avoiding this roadblock to success with scalable control systems providing embedded and tightly integrated advanced control and operations software. Best-in-class systems have model predictive control and other advanced process control solutions built in. Those same systems will also be able to easily integrate with simulation software to create initial configuration and tiebacks automatically in a matter of minutes. These are just a few examples of the technology that is embedded and easily integrated into modern, scalable control systems.
Many of the most successful companies are also finding increased success by selecting control solutions with embedded, industry standard communication protocols. This embedded functionality provides additional flexibility and risk reduction. If at a late stage they need a package or device that uses PROFINET (for example) instead of traditional I/O, they can simply turn it on in the existing controller software, rather than adding hardware and additional engineering (Figure 3).
Successful trailblazers need supportive technology
Over the coming years, lithium battery manufacturing will continue to innovate and grow. As a result, it is an industry ripe with opportunity. That opportunity will come fastest and easiest to the organizations that build from the earliest stages with flexibility and scalability in mind. The technologies exist today to design for scalability from the very first moments of a pilot. Those organizations that do so will capture competitive advantage and usher in the future of battery technology.
All figures courtesy of Emerson
About The Author
Kenny Marks is a senior business development manager for Emerson. In this role, he is responsible for industry development and key account leadership and support within the lithium battery value chain. Marks has been with Emerson for 11 years, with previous roles in product marketing, technology and process automation engineering. He holds an Executive MBA from the University of Texas, and bachelor’s degrees in computer and electrical engineering from West Virginia University.
Did you enjoy this great article?
Check out our free e-newsletters to read more great articles..
Subscribe